Laser Cutting in the Medical Device Manufacturing Industry
The medical device industry has undergone a major overhaul following the 2009 Affordable Care Act. The need for lower-cost health care comes along with increased demand for high-quality, affordable equipment with shorter lead times. As such, the medtech field is growing, and there’s a gap in the market for laser cut machining, which savvy laser engravers can turn their hands to. If you’re already in the medical device field, a laser cutting machine could help you increase output.
In this comprehensive guide to medical device laser cutting, we explore the applications of laser power and demonstrate the benefits of laser technology in the medical field.
What Is a Laser Cutter?
A laser cutting machine uses a focused laser beam to alter the surface of a variety of materials, either cutting, marking, etching or engraving. There are several different types of lasers — fiber lasers, CO2 lasers and Nd:YAG lasers — all of which can be used for medical laser cutting.
Laser technology is used extensively in the medical field due to its ease of use and high-power output. However, in the past, laser engraving machines were the reserve of large industrial enterprises that could afford the equipment. Today, practically anyone with an entrepreneurial spirit can set up their own laser cutting business.
Laser cutting is an excellent tool for the medical industry due to being a contactless high-speed cutting, marking or etching process with high resolution. There are extensive codes and regulations within the medical technology industry, and lasers can help ensure compliance. Read on to find out everything you need to know about the laser engraving and cutting process in medtech.
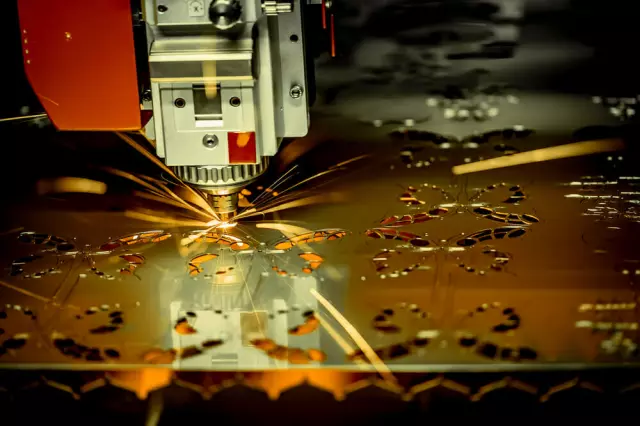
Material Thickness
Laser cutters work with a broad range of materials of varying thicknesses. In most instances involving laser cutting medical devices, you’d use a pulse setting to finish delicately sized and high-tolerance parts like stents and catheters. The frequency and duration of the pulses dictate the maximum thickness and cutting speed, in addition to feature size. The thinner the feature, the finer and slower the cut has to be. When a material is finer, laser technicians use high pulse frequency and short duration.
Material Selection
CO2 lasers can mark coated stainless steel or coated aluminum, but a higher powered laser is usually required for cutting materials like nitinol, MP35N and other metals.
You can use laser technology to cut substances like platinum iridium for electrodes and titanium for implants — but expert skills are required to set up the machine. It’s possible to ease runway and thermal build-up with titanium, using a pulsing output from the laser tube and working with fully or semi-inert gas. The main issue with laser cutting platinum iridium is dross on the opposing side of the cut. Again, by pulsing the laser, you have enhanced control over the heat output.
Top Five Uses of Precision Laser Systems in Medical Device Manufacturing
There are many ways to use lasers within the medical device industry, including ablation, welding, micromachining, marking, cutting and more.
Laser Cutting Technology
Gas assist laser cutting is the most popular method used for developing medical tools such as hypodermic needles, hypo tubes, stents, cannulas and shaver blades. Gas assist is mainly used alongside a microsecond laser source and has sufficient precision and speed for the correct kerf width and cut quality. That said, when it comes to creating the smallest, most delicate equipment, ablation is necessary due to the need for pulsed laser technology. Ablation can lead to kerf widths and feature sizes in the tens of microns.

Laser Marking
Laser marking is widely used in the dental and medical fields to make parts for equipment such as endoscopic tools, auditory implants, pacemakers and bone screws. The FDA requires such tools to be branded with unique device identifier marks that are corrosion-resistant. This process is known as direct part marking, and it’s used in a wide range of industries that operate under strict local, state and federal regulations. The FDA states that marks on multi-use stainless steel medical devices must be:- Capable of going through extensive cleaning passes
- Biocompatible
- Without surface inclusions
- Corrosion-resistant
Material selection determines which type of laser is required for laser marking medical devices, but CO2 lasers are compatible with many relevant materials, including anodized aluminum, coated stainless steel, acrylic and polymer.
Laser Micromachining
Laser micromachining is an industrial process used to texture surfaces and drill holes in tools such as micro-instruments, implants, catheters and needles. In most cases, ultra-short-pulse lasers are used for this application due to the fact that short pulse duration removes material more efficiently with less power, which leads to cleaner cuts that require minimal post-processing.
Micromachining is by no means fast, but it’s ideal for high-precision jobs where motion control is essential.
Laser Welding
When it comes to the most intricate and delicate medical tools, lasers are used for seam welding, micro welding and hermetic sealing. Parts for batteries, endoscopic instruments, surgical blades and pacemakers often require micro welds. Spot welding is used for medical hypo wires, guidewires, hook assemblies and fine springs. Finally, seam welding is usually used with implantable devices.
Laser Ablation
Laser ablation is when a laser is used to remove selected material while keeping the rest intact. It’s being used increasingly in the medical equipment industry for applications relating to micro instruments, micro implants, balloon surface texturing, catheter tip shaping and wire coating removal. Ultrafast, excimer and CO2 diode lasers are most widely used in this instance.
Why Are Laser Cutting Machines Used to Make Medical Components?
Laser cutting machines can be used as cost-effective tools to manufacture high-volume components for implements such as catheters. Using laser technology for this application has a broad array of advantages — let’s take a look at them.
High Precision
Laser medical devices can contribute towards increased precision during surgery because they help doctors make accurate cuts while performing critical procedures. The more precise the implement, the faster the medical professional can get their job done. What’s more, precisely manufactured surgical implements can equal shorter healing times for patients.
Laser-made medical equipment is essential for stents, which are used during surgery and for people with kidney stones. It’s also used to make parts for:
- Valve framers
- Flexible shafts
- Hones
- Vascular clips
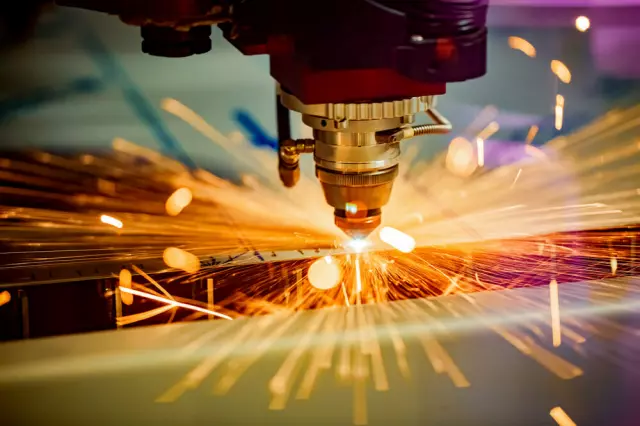
Torque Transfer
Laser cut technology generally uses an interrupted cutting process, with a direct connection that ensures healthy torque response in-vivo.
Fast
One of the main benefits of using a laser cutter for medical devices is the fast turnaround time. Shorter lead times and increased efficiency during surgical procedures can make clinicians’ practices more profitable.
Cost-Effective
In addition to being fast, laser engraving technology is cost-effective due to the high accuracy and relatively low power output.
Customized
Traditional coiling and braiding techniques make it more challenging to create tools that require flexibility on one end and stiffness on the other. Laser cut technology has the power to customize output according to clinical demands.
Versatile
You can use laser cutting machines on glass, metal, plastic and other materials with ease. This eliminates the need for multiple tools, which cost more money and require additional space.
Flattening
When using braiding and coiling techniques to make catheters, there’s a risk of flattening or misshaping as they move through a patient’s anatomy. Laser cutters create finished tools that are formed as a single tube, which means this is far less likely.
Increased Capacity
Lastly, increased capacity is one of the most important reasons to consider using laser technology to manufacture medical devices. Scaling up can be one of the most expensive and risky pursuits any business goes through, but increased demand in the public and private sector requires many medical teams to increase output. Slowed growth means not being able to provide treatment as efficiently or quickly, which could lead to lost patients.
Laser cutters allow medical manufacturers to upgrade the technology they’re currently using, which in turn means health care providers offering shorter waiting times and increased capacity. Laser cut medical devices have faster turnaround times but maintain the required quality standards.
Traditional laser engraving, marking and etching processes require more time, which slows down operations for medical providers. As a medical device manufacturer, you can offer a better service that improves your clients’ operational efficiency and potentially increases revenue. The population is growing and aging, and health care demands are set to continue growing. Laser technology allows you to keep up with growing demand for products, which is a net benefit to everyone.
Benefits of Laser Technology in Medical Device Manufacturing
If you’re a contract manufacturer making tools for the medical device industry, a laser cutter could help you ramp up production and improve operations. Below is a summary of the main benefits of using lasers in the medical sector:
- Laser cutting is safe and requires zero contact between the machinery and the tool itself because the laser is encased in a glass tube.
- Laser machines use inexpensive parts, which boosts their cost-effectiveness.
- Lasers work with a range of materials, including glass, metal and plastic.
- Low power and low maintenance costs make laser cutters energy-efficient and affordable to run.
- Medical devices require tiny parts, and lasers provide the precision necessary to make such delicate and intricate implements.
- Laser technology promotes compliance in an industry as heavily regulated as the medical field.
Medical Device Manufacturing Standards
There are many management standards that apply in the medical device industry, with some of the most common being:
- OHSAS 18001/ ISO 45001
- ISO 27001
- ISO 50001
- ISO 14001
- ISO 13485
- ISO 9001
Upgrade Your Equipment Today
If you’d like to add an affordable, versatile laser cutting machine to your work area, visit Thunder Laser USA today. We deliver high-quality machines ranging from 30 watts all the way up to 130 watts to support a variety of applications. Bed sizes start at 22 inches and go up to 51 inches.